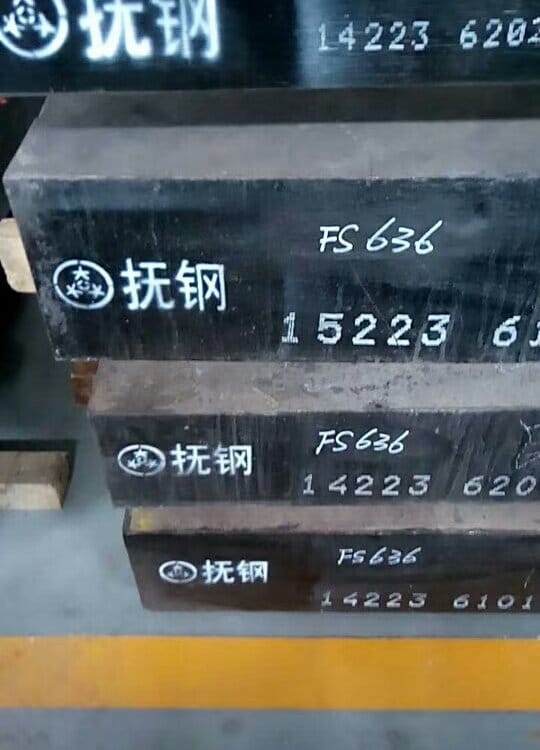
What Is Hot Work Mold Steel? Hot work mold steel is an alloy tool steel used for the hot deformation processing of metals. Hot work mold steel needs to work under high temperature and high-pressure conditions for a long time. So, Hot work mold steel needs to have the characteristics of high thermal strength, thermal fatigue, toughness and wear resistance. Hot work mold steel can be used for many hot deformation tools. Such as hot forging molds, hot extrusion molds, mold casting molds, and hot molds. We are a mold steel manufacturer from China. We can supply a variety of Hot work mold steels as well as other types of steel. The following also introduces the Hot work mold steel in detail.
Hot work mold steel properties
Hot work molds are used in extremely harsh conditions. In order to meet the requirements of hot work mold, Hot work mold steel has the following characteristics:
- Good wear resistance. Can withstand high-temperature oxidation and grinding of iron oxide chips.
- Excellent thermal stability. Under high temperature conditions, Hot work mold steel can maintain stable mechanical properties for a long time.
- Good thermal fatigue resistance. Hot work tool steel can be repeatedly heated without premature fracture.
- High temperature strength and good toughness. Hot work molds are subjected to high frequency and high impact force and will not crack easily.
- High hardenability. The high hardenability can make it keep the mechanical properties of the abrasive tool section stable. which can satisfy the large size hot work mold.
- Good thermal conductivity. Good thermal conductivity can reduce the temperature difference inside the abrasive tool. It will not cause the mechanical properties of hot work abrasives to decline due to excessive heat accumulation.
Hot work mold steel composition characteristics
In addition to the C element, the alloying elements that are usually added to the Hot work mold steel are Cr, Ni, W, Mo, V, Mn, and Si. Each alloying element improves the performance of hot work abrasive steel differently.
- Mo, V, etc. are precipitated in the form of carbides during tempering to produce secondary hardening. So that the Hot work mold steel still maintains a relatively high hardness at higher temperatures.
- Cr and Si can improve the oxidation resistance of steel.
- Cr, Mn, Si, Ni alloy elements are used to strengthen ferrite and improve hardenability.
- Mo alloying element is to prevent temper brittleness.
- Cr, W, Si alloy elements can increase the phase transition temperature. Thereby improving its thermal fatigue resistance.
Classification and application of hot work mold steel
Hot work mold steel can be classified according to alloying element content and properties after heat treatment. The common types are as follows:
- Low heat resistance and high toughness hot work mold steel
- Medium heat-resistant and high-toughness hot work mold steel
- High heat resistance and high toughness hot work mold steel
- Special purpose hot work mold steel
The properties and applications of each type of hot work mold steel are described below.
1.Properties and application of low heat resistance and high toughness hot work mold steel
Low heat resistance and high toughness hot work mold steel is mainly used for hot work mold with large impact load. Common hot work mold steels include 5CrMnMo and 5CrNiMo.
Low heat resistance and high toughness hot work mold steel has high hardenability, good impact toughness, good thermal conductivity and high thermal fatigue resistance. It withstands working conditions that can withstand rapid cold and rapid heat at around 400°C.
At the same time, this type of steel also needs good forging, machining, heat treatment process performance. and good surface strengthening properties.
Of course, the hardenability of some earlier hot work mold steels cannot meet the requirements of large-section hammer forging molds. And the operating temperature cannot exceed 500 °C. So, some hot work mold steels with higher alloying elements have also been developed. Such as 3Cr2MoWVNi, 45Cr2NiMoVSi, 5Cr2NiMoVS and other steels. Their thermal stability and lifespan are greatly improved.
2. Properties and applications of medium heat-resistant toughness steel
The characteristics of the medium heat-resistant toughness steel are that the C content is relatively low. More alloying elements are added. For example, carbide-forming elements such as Cr, W, Mo, V, etc.
Cr and Mo elements improve the hardenability of steel.
The V element makes the steel have better sensitivity to overheating. It is very effective for improving the hot hardness and thermal strength of the mold. At 500~600°C, the steel has high hardness, thermal strength and wear resistance, up to 650°C.
Common medium heat-resistant toughness steel hot work mold steels include 4Cr5MoSiV1, 4Cr5MoSiV, 4Cr3Mo3SiV,
3Cr3Mo3W2V, 4Cr5W2VSi, etc.
Medium heat-resistant toughness steel can be used to manufacture hot extrusion molds, precision forging molds, non-ferrous metal mold-casting molds, etc.
3. Properties and Applications of High Heat Resistance Steel
Compared with other hot work mold steels, high heat resistance hot work mold steels have higher alloying elements. The mass fraction of alloying elements in most high heat-resistant steels is 8% to 10%, and some are up to 11%.
High heat resistance steel has high heat resistance and can work at high temperature of 600~700°C. At the same time, it has high hardenability and high fatigue resistance fracture toughness. But, its plasticity, toughness and cold fatigue resistance are lower than those of medium heat and tough steel.
High heat resistance hot work mold steel is suitable for high requirements on heat resistance and wear resistance. But, molds with lower toughness requirements and less complex shapes. For example, press upsetting molds, mold casting molds, and hot work molds that work under higher operating temperatures and high wear conditions. It can also be used on extruders for processing high-strength steel, stainless steel, titanium alloys and other molds with a size of less than 150mm.
The traditional high heat resistance hot work mold steel is 3Cr2W8V steel. If the traditional high heat-resistant hot work abrasive steel is improperly smelted, the ingot is large. The mold temperature is too high, the mold will be brittle and scrapped. To solve such problems, new steel grades have also been developed: HD steel and Y-series steel.
HD steel is a new type of high heat-resistance steel developed to adapt to the working temperature of around 700°C. The common HD steel is 4Cr3Mo2NiVNb. On the basis of 4Cr3Mo3V steel, it reduces the content of Mo and V in the steel. And improves the room temperature, high temperature toughness and thermal stability of the steel. Under the same hardness, the fracture toughness of HD steel is 50% higher than that of 3Cr2W8V steel. The thermal fatigue resistance and thermal wear performances are 1 time and 50% higher respectively. And the service life of the hot extrusion mold made with it is also higher than that of 3Cr2W8V steel.
Y series mold steel is a new type of steel developed for mold-casting models combined with various national mineral resources. The common one is Y10 mold steel (4Cr5Mo2MnVSi). Y10 hot work mold steel has good hardenability. Because of the addition of Si and Mn elements, its matrix strength is also improved. This mold steel is mainly used for aluminum alloy mold-casting molds. Y series steel is used in mold-casting mold, and its service life is greatly improved compared with 3Cr2W8V steel.
4. Properties and Application of hot work mold steel for Special Purposes
With the development of new technologies and new processes, higher requirements are also placed on molds. Ordinary hot work mold steel can not meet some special requirements. So, special performance steels must be used to make hot work molds. So that the molds can meet their technical requirements and greatly improve their service life. The following also introduces several commonly used special-purpose hot work mold steels.
4.1 Austenitic hot work mold steel
Austenitic hot work mold steel generally contains high alloying elements such as Cr, Ni, and Mn. According to the content of alloying elements, it can also be divided into chromium-nickel austenite and high manganese austenite.
The microstructure of austenitic hot work mold steel is relatively stable. It does not undergo phase change during heating and cooling and has high temperature strength and heat resistance. The disadvantage is that the coefficient of linear expansion is large. The thermal conductivity is poor. This reduces the thermal fatigue performance of the steel. Not suitable as a mold material for strong water cooling.
Chromium-nickel austenitic stainless heat-resistant steel has good oxidation resistance. It can be used in titanium alloy creep forming molds, strong corrosive glass-forming molds, and mold-casting cores and other hot-working molds. High manganese austenitic heat-resistant steel is suitable for making molds with an operating temperature higher than 700°C. But lower than 900°C, high working stress and simple shape. For Examples, copper alloy extrusion mold, steel or high temperature alloy extrusion mold, powder sintering mold, etc.
4.2 Carbide and Steel Bonded Carbide
Cemented carbide has high hardness and good wear resistance. The working temperature can reach 800~1000°C. This steel has high elastic modulus, small expansion number and good chemical stability. It is used to make some hot work molds, and its life is more than 10 times higher than that of mold steel.
Because cemented carbide has high hot hardness and wear resistance. It also has good thermal stability, oxidation resistance and corrosion resistance. So, it can be used to make some hot work molds. Tungsten-cobalt cemented carbide can be used for hot-cutting mold, mold-casting mold, and hot extrusion punch or mold with high working temperature. Steel-structured hardware alloys can be used to make hot extrusion molds, hot punching molds, and hot flat forging molds.
4.3 Precipitation hardened hot work mold steel
Precipitation Hardened hot work mold steel has low carbon content. Some precipitation hardening alloying elements are added. Such as V, Ni, Mo and so on. This steel has good toughness and machinability, and can be used for fine machining of the cavity.
A typical precipitation hardening hot work mold steel is 2Cr3Mo2NiVSi steel. It is suitable for making forging molds using temperatures between 500~600°C. The service life of the mold made of 2Cr3Mo2NiVSi steel is doubled compared with that of American H11 steel.
4.4 High-speed steel type heat-resistant mold steel
When high-speed steel is used as a hot work mold, its working temperature reaches 600~700°C. This steel has high strength and good hot hardness, but poor toughness. The service life of high-speed steel type heat-resistant mold steel has been greatly improved. Especially for high-temperature punches, high-speed steel is more advantageous.
High-speed steel type heat-resistant mold steel can be used to manufacture cold working molds and hot stamping punches, extrusion molds, hot forging molds, and hot forming rolls that work at high temperatures.
4.5 Cold and hot base steel
The base steel for both hot and cold use has good technological performance, and the strength and toughness are significantly improved. It is widely used in the manufacture of cold and hot deformation molds that require high load, high speed and impact resistance.
The base steels that can be used as hot and cold molds are 6W8Cr4VTi, 6Cr5Mo3W2VSiTi, 6Cr4-Mo3Ni2WV, 5Cr4W5Mo2V, etc. The hot extrusion mold and hot forging mold are made of base steel. Its service life is higher than that of the mold made of 3Cr2W8V steel.
4.6 Maraging heat-resistant steel
The C content of maraging steel is very low and the Ni content is relatively high. This steel has ultra-high strength, good plasticity, good wear resistance, high fracture toughness and high heat resistance. Works strong below 500°C
The degree of temperature does not decrease, the high temperature fatigue strength is high, and the oxidation resistance is high. It has good low-temperature performance and corrosion resistance.
Maraging steel contains high content of precious alloying elements and is expensive. So, it is only used to manufacture small, precise and complex long-term mold-casting molds, precision forging molds and mandrels of mold-casting molds.
As a hot work mold steel manufacturer. We can provide all kinds of hot work mold steel and other types of steel according to customer needs. If you have any steel needs, you can always consult us.
Popular hot work mold steel
Name | https://www.jcmetalchina.com/hot-work-mold-steel/ |
5CrNiMoV | https://www.jcmetalchina.com/steel/5crnimov/ |
5Cr4W5Mo2V | https://www.jcmetalchina.com/steel/5cr4w5mo2v/ |
6Cr4Mo3Ni2WV | https://www.jcmetalchina.com/steel/6cr4mo3ni2wv/ |
5CrMnMo | https://www.jcmetalchina.com/steel/5crmnmo/ |
4CrMnSiMoV | https://www.jcmetalchina.com/steel/4crmnsimov/ |
5Cr2NiMoVSi | https://www.jcmetalchina.com/steel/5cr2nimovsi/ |
4Cr5MoSiV | https://www.jcmetalchina.com/steel/4cr5mosiv/ |
4Cr5MoSiV1 | https://www.jcmetalchina.com/steel/4cr5mosiv1/ |
4Cr5W2VSi | https://www.jcmetalchina.com/steel/4cr5w2vsi/ |
8Cr3 | https://www.jcmetalchina.com/steel/8cr3/ |
3Cr2W8V | https://www.jcmetalchina.com/steel/3cr2w8v/ |
3Cr3Mo3W2V | https://www.jcmetalchina.com/steel/3cr3mo3w2v/ |